Разработка участка по ремонту тележек локомотивов в локомотивном депо Хабаровск 2
1.2.3 Определение величины технологического процесса
Для ритмичной работы цеха необходимо иметь оборотный фонд исправных агрегатов и узлов (технологический и страховой запасы).
Технологический запас (Т3) создается для сокращения производственного цикла ремонта базового объекта (тепловоза, дизеля, тележки и т. д.) в тех случаях, когда время, затрачиваемое на ремонт узла, превышает
срок, предусмотренный графиком сборки тепловоза.
Технологический запас ТЗ в единицах при ремонте ТР-3 определяется по формуле
ТЗ = (Т1-Т2)Мтр-3 K / Fо,
где Т1 – время продолжительности ремонта снимаемого узла, ч;
Т2 - время с момента снятия объекта до постановки, ч;
K = 2 – количество однотипных сменных объектов на секцию тепловоза.
Продолжительности Т1 и Т2 берутся из таблицы 2.3.
Таблица 2.3 - Время Т1 и Т2 применяемое в цехе ТР-3
Объекты ремонта |
Продолжительность ремонта Т1, ч |
Время на снятия объекта и постановку Т2, ч |
Тележка |
60 |
36 |
ТЗ = (60 – 36)*61*2 / 1881,6= 1,56 шт.
1.2.4 Расчет потребного штата ремонтного подразделения локомотивного депо
Расчет потребной численности производственной рабочей силы, необходимой для ремонта тепловозов и его узлов, выполняется в соответствии с годовой программой ремонта и трудоемкостью работ, т. е. затратой рабочей силы в человеко-часах на единицу ремонта.
Явочное количество производственных рабочих всех профессий ремонтного подразделения Кря, чел определяется по формуле
Кря = Мтр-3 Чч / Fря,
где Чч = 100 – затрата чел.-ч на секцию.
Кря = 122*100 / 1960= 7 чел.
Списочное (штатное) количество рабочих ремонтного подразделения, в которое входят и рабочие, находящиеся в отпуске, командировке, больные и т.д. определяется по формуле
Крс = Мтр-3 Чч / Fрс,
Крс = 122*100 / 1679,6 = 7 чел.
Квр = 7*0,15 = 1 чел.
Итого 7+1 = 8 чел.
1.3 Организация производственного процесса в ремонтном подразделении
Схема разборки рамы тележки представлена на рисунке 1.4
Рисунок 1.4 – Схема разборки рамы тележки
1.3.1 Контроль состояния рамы тележки и методы устранения дефектов
1.3.1.1 Дефект – трещины
Трещины появляются главным образом в зонах высоких механических нагрузок и в зонах концентрации напряжений. Трещины выявляются визуальным методом и методом цветной дефектоскопии. Визуальный метод заключается в осмотре рамы тележки невооружённым взглядом. В отдельных случаях применяются лупы 5…10ти кратного увеличения. Цветная дефектоскопия применяется для контроля состояния деталей из черных и цветных металлов, которые имеют трещины, выходящие на поверхность. В основе метода лежит способность некоторых жидкостей, имеющих чрезвычайно высокую капиллярность, слабое поверхностное натяжение и малую вязкость, проникать в самые тончайшие трещины. На раму тележки после очистки и обезжиривания наносят проникающую жидкость. По истечении 5 – 10 минут, когда жидкость проникнет глубоко в трещины и поры, раму промывают проточной холодной водой или 5%ым раствором кальцинированной соды. Затем раму сушат и покрывают мелким сухим микропористым порошком силикагеля или водным раствором каолина или мела (на 1л. воды – 600…700 грамм каолина или 300…400 грамм мела). Нанесенный на деталь каолин или мел должен высохнуть. Если трещина, то проникающая жидкость из неё под действием капиллярных сил заполняет микропоры силикагеля (каолина или мела), который действует, как промокательная бумага. В результате над трещиной появляется цветная линия, копирующая форму и размеры трещины. По ширине этой линии (жилки) судят о глубине трещины – чем она шире, тем глубже трещина. В качестве проникающей жидкости может служить состав, приготовленный из 80% керосина, 20% скипидара и 15 грамм краски “Судан - 4” на 1 литр смеси. Можно применять состав из 75% керосина, 20% трансформаторного масла и 5% антраценового масла, и другие составы. Наиболее активными индикаторами являются составы тубикол и норикол. При заварке трещин в сварных швах рамы тележек без выхода на основной металл необходимо концы трещин засверлить сверлом диаметром 3 – 5 мм с раззенковкой отверстий; трещину разделывают пневматическим зубилом по всей длине под V-образный шов, при этом старый металл должен быть полностью удалён. Заварку всех трещин на раме производить электродами типа Э42А, Э46А или Э50А в нижнем и вертикальном положении, потолочная сварка не допускается. Род тока – постоянный, обратной полярности. Диаметр электродов 3, 4, 5 мм. При заварке металл вблизи трещины должен быть нагрет газовой или нефтяной горелкой до температуры 300 – 4000 С. После заварки с целью снятия внутренних напряжений производят нормализацию сварного шва, для чего металл медленно прогревают до температуры 6000 С, и ещё медленнее охлаждают, защитив нагретое место асбестовой изоляцией. По окончании сварочных работ шов зачищают шлифовальной пневматической машинкой. При заварке сквозных трещин и варке вставок в боковину рамы трещины разделывают газовым резаком с последующей разделкой мест пневматическим зубилом Х-образно. При больших зазорах разрешается вваривать вставки из стали Ст3. Заварку трещин, разделанных Х-образно, рекомендуется выполнять одновременно двум сварщикам – по одному с каждой стороны полотнища рамы. После заварки зазора слои должны накладываться вертикально снизу-вверх, каждый слой должен защищаться.
1.3.1.2 Дефект - износ шкворневого устройства
![]() |
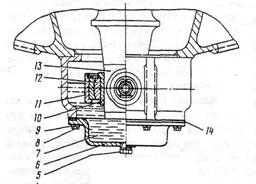
1 – брус шаровой связи; 2 – прокладки; 3 – сегментообразные упоры; 4 – валики; 5 – пробка; 6 – крышка; 7 – масло; 8 – болты; 9 –пружинные шайбы; 10 – латунная втулка; 11 – корпус; 12 – шар; 13 – шкворень; 14 – прокладка.
Рисунок 2.5 - Шкворневой узел в сборе
Диаметр шара по наружной поверхности должен быть в эксплуатации менее 217 мм. Износ сегментообразных упоров допускается не более 2 мм, а зазор между ними и корпусом, который регулируют путем постановки прокладок, не более 1,5 мм. Суммарный зазор между шаром и вкладышем, а также между упором и втулкой в шкворневом брусе не должен быть в эксплуатации более 2 мм. Проверить в брусе шаровой связи резьбу М12 для крепления крышки и резьбу М30 для крепления стаканов противоотносного устройства.
1.3.1.3 Дефект – износ поверхности кронштейна подвески ТЭД
Износ выявляется микрометрическим методом. Для этого следует использовать микрометрический нутромер. Нутромер помещается между накладками в поясе а-а, который будет располагаться по широкой стороне подвески. Размер должен быть не более 311мм.
Другие рефераты на тему «Транспорт»:
Поиск рефератов
Последние рефераты раздела
- Проект пассажирского вагонного депо с разработкой контрольного пункта автосцепки
- Проектирование автомобильных дорог
- Проектирование автотранспортного предприятия МАЗ
- Производственно-техническая база предприятий автомобильного транспорта
- Расчет подъемного механизма самосвала
- Системы автоблокировки
- Совершенствование организации движения и снижение аварийности общественного транспорта в городе Витебск